Company News
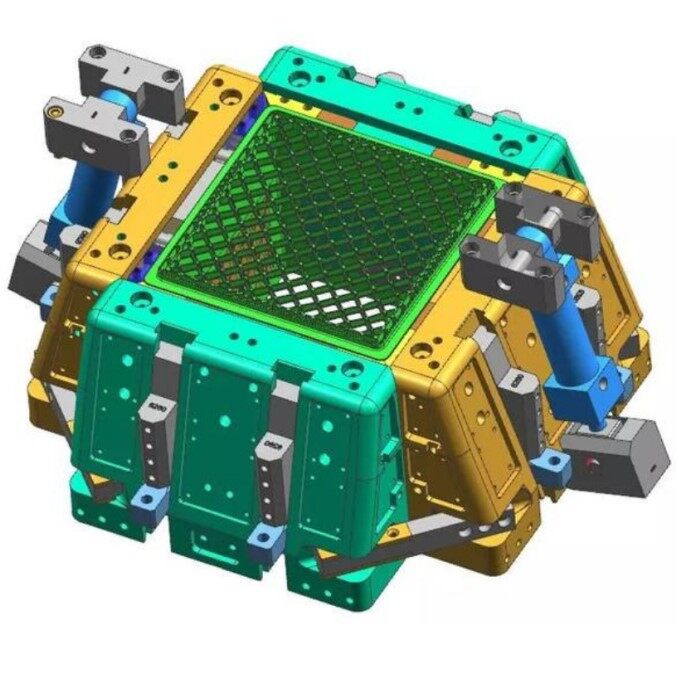
http://www.gokotechnology.com/
With the continuous development and innovation of the times, the competition in the manufacturing industry has become more and more fierce. The ability of enterprises to provide customers with personalized high-quality products with high efficiency and low consumption in the shortest possible time has become a symbol of enterprise competitiveness. Some experts said that the mold quality will directly affect the product quality, output, cost, the cycle of new product production and old product renewal, the speed of enterprise product structure adjustment and market competitiveness. Therefore, the economic situation puts forward higher and higher requirements for the mold quality. How to improve mold quality more reasonably is the key to the leap of manufacturing industry. How to make the mold produce qualified parts for a longer time and more times under the conditions of high precision, low cost and high efficiency has increasingly become the focus of people's attention.
1、 Develop high-quality alternative steel
Steel is an irreplaceable product with high energy consumption. The effect of energy conservation and emission reduction brought by improving quality and performance and reducing steel consumption is far greater than the potential in the process of steel production.
In recent years, China's iron and steel industry has achieved remarkable results in energy conservation and emission reduction, but the greatest energy-saving potential of China's iron and steel industry is not in the steel production process, but in improving steel quality and reducing steel consumption. This is because the quality and performance of steel in China are generally low. In order to ensure the service performance, users have to replace fine with coarse.
Taking automobile as an example, the proportion of high-quality and high-strength steel used in passenger cars in China accounts for only 21%, twice the international average of 40% - 50% and one to three times the European advanced level (47% - 80%). Due to the use of steel, the self weight of domestic passenger cars is more than 10% higher than that of European and Japanese cars, with an average fuel consumption of 8.13 liters per 100 kilometers, 23.2% higher than that of Europe (6.6 liters) and 37.8% higher than that of Japan (5.9 liters). China's shipbuilding industry is similar. The average steel consumption per DWT is 300 kg, 36% higher than that of Japan (220 kg), which also increases the operating fuel consumption. There is also a huge potential for material saving and energy saving in the mold field. For example, replacing low-grade steel standards with medium and high-grade steel can save 10% - 20% of steel; Using light high-strength alloy tool steel instead of ordinary steel can save 30% - 50% of steel. According to experts, in 2010, China's consumption of more than 600 million tons of steel will be reduced by 100 million tons. If this goal is achieved, only the steel production process can consume at least 62 million tons of standard coal and reduce carbon dioxide by more than 160 million tons. At the same time, the use of high-strength steel vehicles and ships will greatly reduce the energy consumption of these materials and reduce the pollution of these transportation industries by - 700 million tons. In addition, reducing 100 million tons of steel can also reduce the consumption of iron ore by more than 150 million tons, equivalent to a quarter of the imported ore last year, which can greatly alleviate the plight of imported ore in the iron and steel industry.
2、 Optimize process structure scheme
The designer of the part must consider the technical requirements of the part and its structure must meet the process and feasibility of mold manufacturing.
3、 Pay attention to die steel material selection
This is the most important step to improve the mold quality. Many factors need to be considered, including the selection of mold steel materials, the usability and safety of mold structure, the machinability of mold parts and the convenience of mold maintenance. These should be considered as comprehensively as possible at the beginning of design.
① The selection of die steel materials should not only meet the customer's requirements for product quality, but also take into account the cost of materials and their strength within the set cycle. Of course, the material should be selected according to the type of die, working mode, processing speed, main failure forms and other factors.
② When designing the die structure, try to be compact and easy to operate, and ensure that the die parts have sufficient strength and stiffness. When the die structure allows, the corners of each surface of die parts shall be designed as fillet transition as far as possible to avoid stress concentration; For concave die, cavity, part of punch and core, combined or inlaid structure can be used to eliminate stress concentration; For slender punch or core, appropriate protective measures shall be taken in structure; The cold stamping die shall be equipped with devices to prevent blocking of parts or wastes (such as ejector pin, compressed air, etc.). At the same time, we should also consider how to reduce the impact on the die quality caused by the wear of sliding mating parts and frequent impact parts in long-term use.
③ In the design, it is necessary to reduce the scope of disassembly and assembly when maintaining a certain part, especially when replacing vulnerable parts, and reduce the scope of disassembly and assembly as much as possible.
4、 Pay attention to the machining accuracy of manufacturing process
This is also an important part to ensure the quality of the mold. The machining method and machining accuracy in the mold manufacturing process will also affect the service life of the mold. The accuracy of each part directly affects the overall assembly of the die. In addition to the impact of the accuracy of the equipment itself, it is necessary to improve the processing method of the parts and the technical level of the fitter in the process of die assembly to improve the processing accuracy of the die parts; If the overall assembly effect of the die fails to meet the requirements, the probability of the die moving under abnormal conditions will be improved in the die test, which will have a great impact on the overall quality of the die. In order to ensure that the mold has good original accuracy - original mold quality, in the manufacturing process, we should first reasonably select high-precision machining methods, such as EDM, wire cutting, NC machining, etc. at the same time, we should pay attention to the accuracy inspection of the mold, including the machining accuracy and assembly accuracy of mold parts and the accuracy of the mold through the comprehensive inspection of mold test acceptance. During inspection, high-precision measuring instruments shall be selected as much as possible. For those die parts with complex surface structure, if ordinary ruler and vernier card are used, accurate measurement data cannot be achieved. At this time, precision measurement equipment such as coordinate measuring instrument shall be selected to ensure the accuracy of measurement data.
-
silica sol casting butterfly valve precision casting parts
-
CNC machining parts from rough casting valves
-
cast steel soft-sealing sluice valves manufacturing
-
steel CF8M sluice valve manufacturer
-
steel CF8M hydraulic brake valve body
-
stainless steel CF8M brake valve
-
HL Parts | Customized Anodizing Aluminum Parts Mechanical Metal CNC Processing Services CNC Turning And Milling Part Service
-
HL Parts | Factory Custom Motor Cover CNC Machining Anodic Oxidation Parts
-
HL Parts | Custom CNC Machining Service,CNC Machining Parts, CNC Milling Machined Anodized Aluminum Parts Rapid Prototype
-
HL Parts | Black Bakelite Corrugated Hand Wheel Threaded Keyway Valve Switch Knob Female Star Knobs
-
HL Parts | Custom high precision alloy aluminum stainless steel hot forging die casting machining service grey iron sand casting
-
HL Parts | Custom metal Custom Factory Metal Die Cast Metalworking Cast Iron Precision Casting Parts
-
HL Parts | Custom Made High Precision Automatic Micro CNC Machininig Service Aluminum Stainless Steel Brass Milling Turning Parts
-
HL Parts | Mdf Acrylic Hookah Machininig Machine Service Wood Processing Shop Foam Service Services Aluminium Cnc Cnc Machining Part
-
HL Parts | Custom Brass CNC Accessories Metal Spare Precision Turning Mechanical CNC Machining Products Copper Services Parts Supplier
-
HL Parts | Custom Milling Machining Parts Precision Aluminum Milling Part For Bicycle Accessories
-
HL Parts | High Speed Door Zipper Pvc Accessories Or Zipper High Speed Door Accessories High Speed Roll-Up Door Motor/Operator
-
HL Parts | BAP300R End Mill Tool Holder CNC Metal APMT1135 Carbide Insert Arbor Right Angle End Milling Cutter Holder
-
HL Parts | Manufacturer supply high quality Aluminum Handle Brass Valve Brass Low Price Steel Ball Brass Ball Valve
-
HL Parts |EDM Service Huizhou High Precision Aluminum Manufacturing Casting Industry Machined Parts Chemical Machinery Parts Finish
-
HL Parts | CNC RF Connector Accessories TNC Coax Cap male female TNC Dust Cap Protective Cover with Chain
-
HL Parts | Oem Custom Aluminum Stainless Steel Brass Titanium Plastic Cnc Precision Machining Milling Turning Lathe Part Machining Service
-
HL Parts | Custom High Precision Cnc Metal Machining 5 Axis Stainless Steel Brass Aluminum Titanium Cnc Milling Turning Parts
-
HL Parts | Cnc Turning Milling Metal Machining Precision Parts Aluminium Brass Stainless Steel Custom CNC Process Turning Parts